Kontenery morskie w spedycji – rodzaje, zastosowania, innowacje
Kontenery morskie zrewolucjonizowały globalną logistykę, stając się nieodłącznym elementem międzynarodowej wymiany towarowej. Choć ich powszechne wykorzystanie rozpoczęło się dopiero w latach 50. XX wieku, w ciągu kilku dekad kontenery diametralnie zmieniły sposób organizacji transportu. Za początek ery konteneryzacji uznaje się rok 1956, kiedy to amerykański przedsiębiorca Malcolm McLean wysłał pierwszy statek z ładunkiem umieszczonym w zunifikowanych metalowych skrzyniach. Od tamtej pory nastąpił dynamiczny rozwój tej technologii – dziś dziesiątki milionów kontenerów krążą po świecie, obsługując znaczną część handlu międzynarodowego.
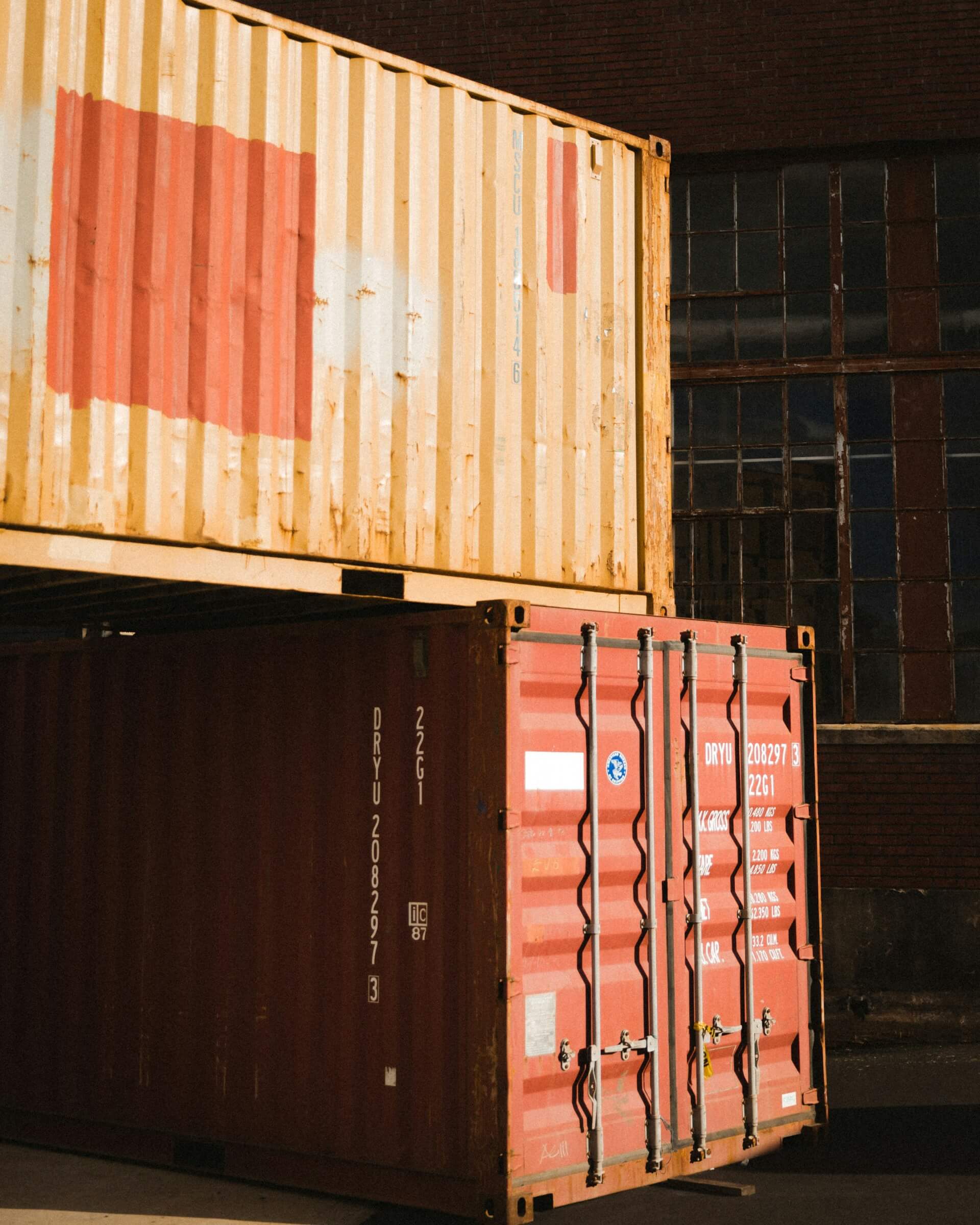
Historia i znaczenie konteneryzacji
Wprowadzenie kontenerów przyniosło logistyczną rewolucję. Przed standaryzacją ładunki transportowano głównie luzem lub w drobnych opakowaniach, co wymagało czasochłonnego przeładunku każdej sztuki towaru z jednego środka transportu na inny. Kontenery pozwoliły skonsolidować drobniejsze przesyłki w większe jednostki transportowe. Dzięki temu przeładunek został znacznie uproszczony, a ryzyko uszkodzeń czy zagubienia towaru – ograniczone. Standaryzacja kontenerów (wprowadzenie jednolitych wymiarów i punktów mocowania) umożliwiła z kolei płynne wykorzystanie tych samych metalowych skrzyń w różnych gałęziach transportu: morskiego, kolejowego i drogowego. To właśnie modułowość i powtarzalność kontenera sprawiły, że załadunek stał się szybszy, a fracht tańszy. Szacuje się, że dzięki konteneryzacji koszty transportu towarów spadły na tyle, iż opłacalny stał się handel na odległość, co znacząco napędziło globalizację gospodarki w drugiej połowie XX wieku.
Standardy i intermodalność
Kluczem sukcesu kontenerów okazały się międzynarodowe normy ISO, które ujednoliciły ich rozmiary oraz wyposażenie. Typowy kontener morski ma stalową konstrukcję o zunifikowanych narożach zaczepowych (tzw. corner castings), co pozwala na bezpieczne podnoszenie dźwigami i mocowanie na pokładach statków czy naczepach. Najpowszechniejsze długości to 20 i 40 stóp, a wysokość standardowa wynosi 8 stóp 6 cali (ok. 2,6 m) lub 9 stóp 6 cali w wersjach podwyższonych. Dzięki temu zestandaryzowaniu kontener może być łatwo przenoszony z żurawia portowego na wagon kolejowy, a następnie na naczepę ciężarówki, bez konieczności przeładowywania zawartości. Ten płynny transfer między różnymi środkami transportu to intermodalność, która stała się fundamentem nowoczesnej spedycji. Operatorzy logistyczni mogą planować trasy „od drzwi do drzwi” wykorzystując jeden zamknięty kontener przez całą drogę – od fabryki nadawcy aż do magazynu odbiorcy – co zwiększa efektywność oraz bezpieczeństwo dostaw.
Zalety i wady transportu kontenerowego
Zalety konteneryzacji
Upowszechnienie kontenerów przyniosło branży TSL (transport–spedycja–logistyka) szereg wymiernych korzyści. Przede wszystkim znacznie obniżono jednostkowy koszt przewozu towarów dzięki efektowi skali – jeden statek jest w stanie jednorazowo zabrać tysiące kontenerów, co rozkłada koszty rejsu na wielu załadowców. Transport kontenerowy cechuje się bardzo dużą uniwersalnością: w standardowej skrzyni można przewozić niemal każdy rodzaj ładunku – od wyrobów przemysłowych, przez ubrania i zabawki, aż po żywe zwierzęta czy materiały niebezpieczne (oczywiście przy zachowaniu odpowiednich procedur). Kontener zapewnia również lepsze zabezpieczenie towaru niż tradycyjny transport konwencjonalny. Ładunek jest zamknięty w stalowej skrzyni, chroniony przed warunkami atmosferycznymi i zabezpieczony przed kradzieżą plombą na drzwiach. Mniej czynności przeładunkowych przekłada się na mniejsze ryzyko uszkodzeń mechanicznych – towary nie są wielokrotnie przerzucane z miejsca na miejsce, lecz pozostają unieruchomione wewnątrz przez całą trasę. Kolejną zaletą jest szybkość operacji przeładunkowych w portach: zamiast setek drobnych pakunków, dźwigi przenoszą kilkudziesięciotonowe kontenery w kilka minut każdy, usprawniając obsługę statków. Takie uspójnienie jednostek ładunkowych umożliwiło rozwój złożonych łańcuchów dostaw just-in-time na globalną skalę. Nie bez znaczenia jest też fakt, że transport morski w przeliczeniu na tonę ładunku i kilometr jest najbardziej paliwooszczędnym i ekologicznym ze wszystkich gałęzi – kontenerowiec potrafi przewieźć towary taniej i przy mniejszej emisji CO₂ na jednostkę ładunku niż samolot czy nawet ciężarówka.
Wyzwania i wady
Mimo niewątpliwych zalet, konteneryzacja niesie też pewne wyzwania. Po pierwsze, transport morzem jest stosunkowo wolny – dostarczenie kontenera z Azji do Europy trwa kilka tygodni, co jest istotnie dłużej niż transport lotniczy. Ponadto opóźnienia mogą się nawarstwiać wskutek czynników zewnętrznych: sztormów, zatłoczenia portów czy procedur celnych. Istotnym problemem logistycznym jest zarządzanie pustymi kontenerami. Po rozładunku importu w jednym kraju kontenery muszą wrócić w miejsce, gdzie znów zostaną załadowane – generuje to dodatkowe koszty i bywa nieefektywne, zwłaszcza gdy bilans handlowy między regionami jest zachwiany (np. ogromny eksport z Chin powoduje niedobór kontenerów w Azji i nadwyżki pustych skrzyń w portach zachodnich). Innym ograniczeniem jest konieczność posiadania kosztownej infrastruktury. Nie wszystkie porty świata są dostosowane do obsługi dużych statków pełnych kontenerów – potrzebne są głębokie nabrzeża, suwnice portowe o udźwigu kilkudziesięciu ton i rozbudowane zaplecze magazynowe. Przeciążenie głównych szlaków morskich i hubów portowych bywa problemem, czego przykładem były zatory logistyczne w czasie pandemii. Jeśli chodzi o środowisko, statki kontenerowe mimo wszystko emitują znaczne ilości spalin – branża stoi przed wyzwaniem dekarbonizacji floty. W opinii publicznej pojawiają się też obawy związane z bezpieczeństwem: wypadki takie jak zagubienie kontenerów na morzu czy pożary na statkach budzą niepokój, jednak statystycznie transport kontenerowy pozostaje bardzo bezpieczny. Wyzwanie stanowi ponadto standaryzacja cyfrowa – do niedawna dokumentacja przewozowa opierała się na papierowych konosamentach, co spowalniało obsługę. Podsumowując, mimo pewnych ograniczeń i ryzyk, konteneryzacja jest dziś niezbędnym elementem światowego handlu, a ciągłe innowacje mają na celu minimalizowanie jej wad.
Jesteś zainteresowany naszą ofertą?
Standardowe kontenery morskie
Standardowe kontenery ogólnego przeznaczenia (ang. dry containers) to podstawowe i najczęściej spotykane jednostki w transporcie morskim. Mają zamkniętą, metalową konstrukcję chroniącą ładunek przed czynnikami zewnętrznymi. Służą do przewozu towarów suchych, niewymagających kontrolowanej temperatury ani specjalnych warunków. Poniżej przedstawiono główne odmiany kontenerów standardowych używanych w spedycji wraz z ich charakterystyką.
Kontener 20-stopowy (20′ DV)
Kontener 20-stopowy to najmniejsza z powszechnie używanych jednostek ISO. Jego długość zewnętrzna wynosi około 6,1 m, a standardowa wysokość 2,6 m. Taka jednostka mieści wewnątrz około 33 metrów sześciennych ładunku. Dwudziestostopowe kontenery nazywane są też często jednostkami TEU (Twenty-foot Equivalent Unit), stanowiąc podstawową miarę pojemności statków kontenerowych. Zastosowanie: dzięki kompaktowym wymiarom 20′ idealnie nadaje się do ciężkich ładunków o niewielkiej objętości (np. materiały mineralne w big-bagach, elementy stalowe, części maszyn). Maksymalna ładowność zwykle przekracza 28 ton, co oznacza, że 20′ może unieść więcej masy niż jest w stanie wypełnić objętościowo – to czyni go efektywnym przy transporcie bardzo gęstych towarów. Zalety: łatwość manewrowania – dzięki mniejszej długości kontenerem 20′ wygodniej przemieszcza się go na ciężarówkach w warunkach miejskich i przechowuje na placach składowych. Wady: ograniczona przestrzeń dla ładunków lekkich i obszernych – przy towarach o dużej objętości kontener ten może okazać się zbyt mały pod względem kubatury.
Kontener 40-stopowy (40′ DV)
Kontener 40-stopowy ma długość około 12,2 m i stanowi wydłużoną wersję kontenera standardowego. Jego pojemność wewnętrzna to około 67–68 m³, co pozwala zmieścić dwukrotnie więcej ładunku objętościowo niż w kontenerze 20′. Czterdziestostopowe kontenery są określane także jako FEU (Forty-foot Equivalent Unit) i stanowią podstawę światowej floty kontenerowej – większość kontenerowców jest przystosowana do przewozu właśnie 40-stopowców (liczonych w TEU jako dwie jednostki). Zastosowanie: kontener 40′ sprawdza się przy ładunkach lżejszych lub mniej upakowanych, które wymagają większej przestrzeni. Przykładem mogą być wyroby tekstylne, sprzęt AGD, meble czy artykuły z tworzyw – towary te często wypełniają całą objętość kontenera, zanim osiągną limit wagowy. Standardowy 40-stopowiec ma maksymalną ładowność rzędu 26–27 ton (ze względu na większą masę własną niż 20′). Atuty: znacznie większa pojemność pozwala efektywniej pakować ładunki masowe i drobnicowe – koszty jednostkowe transportu na 1 m³ towaru są niższe niż w przypadku mniejszego kontenera. Minusy: gorsza poręczność – dłuższe kontenery wymagają więcej miejsca przy manewrowaniu i są mniej uniwersalne w zastosowaniach „ostatniej mili” (np. mogą nie wjechać w ciasne ulice czy podwórza).
Kontenery High Cube (HC) i 45-stopowe
Kontenery typu High Cube (HC) to kontenery o podwyższonej wysokości – mierzą 9 stóp 6 cali (ok. 2,9 m) wysokości zamiast standardowych 8′6″. Dzięki temu ich objętość wewnętrzna rośnie o około 10% (dla 40′HC to ok. 76 m³ przestrzeni). High Cube są bardzo przydatne, gdy liczy się każdy dodatkowy centymetr wysokości – np. przy załadunku maszyn, które nie mieszczą się do standardowego kontenera na wysokość, albo lżejszych towarów, które można piętrować wyżej (choćby worki z produktami rolnymi, które wypełnią dodatkową kubaturę). Większość 40-stopowych kontenerów chłodniczych również buduje się w standardzie high cube, aby zrekompensować przestrzeń zajętą przez agregat chłodniczy i izolację. Kontenery HC mają podobną nośność jak zwykłe, lecz nieco większą masę własną (dodatkowa blacha podwyższająca ściany). Wśród kontenerów wysokich występuje też wydłużona odmiana – kontener 45-stopowy (45′ HC). Ma on długość ok. 13,7 m, co czyni go najpojemniejszym standardowym kontenerem. Jego kubatura przekracza 85 m³, dzięki czemu może pomieścić ładunek zbliżony do tego, co zabiera typowa naczepa ciężarowa o długości 13,6 m. Kontenery 45′ są często wykorzystywane w logistyce intermodalnej na trasach europejskich – pozwalają przewieźć większą liczbę palet (zazwyczaj mieszczą 33 palety euro, podczas gdy 40′ mieści 25). Wiele portów i statków jest przygotowanych do obsługi 45-stopowców, choć ze względu na ich długość zazwyczaj lokuje się je na górze stosu kontenerów lub na pokładzie (wymagają odpowiedniego miejsca). Zalety: zwiększona pojemność – przekłada się to na oszczędność kosztów jednostkowych przewozu i redukcję liczby potrzebnych kontenerów przy dużych wolumenach towaru. Wady: ograniczona dostępność (nie wszystkie linie żeglugowe udostępniają 45′ na wszystkich trasach) oraz potencjalne trudności w transporcie lądowym w niektórych krajach (np. limity długości zestawów drogowych).
Kontenery Pallet Wide (PW)
Specyficzną odmianą kontenera ogólnego są kontenery Pallet Wide (PW) o poszerzonej wewnętrznej szerokości. Ich konstrukcja jest tylko kilka centymetrów szersza od standardu ISO – całkowita szerokość zewnętrzna wynosi ok. 2,462 m (wobec typowych 2,438 m), co przekłada się na blisko 2,4 m szerokości wewnątrz. Dzięki temu w kontenerze Pallet Wide mieszczą się obok siebie dwie standardowe palety typu EUR (o wymiarach 120 × 80 cm) bez marnowania przestrzeni. Kontenery te występują głównie jako 40′PW i 45′PW (często równocześnie w wersji High Cube). Ich przeznaczenie to przede wszystkim trasy europejskie i wszędzie tam, gdzie ładunki są w całości paletyzowane na wymiar euro. Dzięki zwiększeniu efektywnej przestrzeni załadunkowej przewoźnicy mogą załadować więcej towaru na jeden kontener, co minimalizuje wożenie „powietrza” wewnątrz. Zalety: poprawa wydajności pakowania ładunków na paletach i redukcja kosztów transportu jednostkowego. Kontenery pallet wide zachowują pełną kompatybilność z infrastrukturą – różnica wymiarów jest na tyle mała, że mogą być obsługiwane identycznie jak zwykłe kontenery. Wady: mimo zgodności ze standardem, kontenery PW są stosunkowo rzadkie poza Europą, co może ograniczać ich dostępność globalnie. W praktyce jednak najważniejsze huby umożliwiają ich obsługę bez problemów.
Kontenery z drzwiami bocznymi i dwudrzwiowe
Niektóre ładunki wymagają ułatwionego dostępu do wnętrza kontenera. Z myślą o nich powstały odmiany kontenerów z dodatkowymi drzwiami. Kontener z drzwiami bocznymi (open side) posiada – oprócz standardowych wrót z jednego krótszego boku – również drzwi na długiej ścianie bocznej. Po ich otwarciu niemal cały bok kontenera jest odsłonięty, co pozwala na załadunek szerokich palet czy maszyn, których nie da się wprowadzić przez wąski otwór z przodu. Natomiast kontener dwudrzwiowy (tunnel) ma pary drzwi na obu krótszych ścianach, dzięki czemu dostęp do ładunku jest możliwy z dwóch stron jednocześnie. Taka konstrukcja ułatwia i przyspiesza rozładunek – można otworzyć kontener z obu końców, co bywa przydatne np. przy przewozie dłużyc (ładunków o znacznej długości) lub podczas składowania, gdy istnieje potrzeba wyjmowania towaru w określonej kolejności. Zarówno wersje boczne, jak i dwudrzwiowe zachowują standardowe wymiary i punkty zaczepienia, ale ich masa własna jest nieco większa (dodatkowe elementy konstrukcyjne). Zalety: większa elastyczność przy załadunku i rozładunku nietypowych ładunków. Wady: minimalnie mniejsza szczelność i izolacja (więcej drzwi to więcej potencjalnych punktów nieszczelności, choć są one dobrze uszczelnione) oraz ograniczona podaż – kontenery z drzwiami bocznymi czy dwustronnymi są rzadsze, przez co ich wynajem może być droższy.
Specjalistyczne rodzaje kontenerów
Oprócz kontenerów standardowych istnieje cała gama kontenerów specjalistycznych, zaprojektowanych z myślą o specyficznych ładunkach i zastosowaniach. Różnią się one budową od zwykłych skrzyń typu dry – niektóre są otwarte od góry, inne mają wbudowane urządzenia chłodnicze lub zbiorniki. Poniżej przedstawiamy najważniejsze typy kontenerów specjalnych używanych w spedycji morskiej, wraz z ich zaletami, wadami i typowym zastosowaniem.
Kontenery chłodnicze (reefer)
Kontener chłodniczy (ang. reefer container) to izolowany kontener wyposażony we własny agregat chłodniczy. Służy do przewozu ładunków wymagających kontrolowanej temperatury, takich jak żywność szybko psująca się (np. owoce, mięso, nabiał), farmaceutyki czy kwiaty. Standardowe kontenery chłodnicze występują w rozmiarach 20′ i 40′ (często jako 40′ High Cube dla większej przestrzeni). Ich jednostka chłodząca może utrzymywać zadaną temperaturę w szerokim zakresie – typowo od około -30°C (dla mrożonek) do +30°C, a specjalne modele nawet od -65°C do +40°C.
Zaletą reeferów jest możliwość stworzenia ruchomej chłodni, która zapewnia ciągłość utrzymania wymaganej temperatury przez całą trasę transportu. Urządzenia chłodnicze zasilane są z sieci – na statkach i w portach kontenery podłącza się do specjalnych gniazd (tzw. reefer points), a podczas transportu lądowego korzysta się z agregatów prądotwórczych montowanych na naczepach. Nowoczesne chłodnie kontenerowe pozwalają na zdalny nadzór nad temperaturą i wilgotnością, alarmując w razie odchyleń. Wadami natomiast są większa masa własna (grube izolacje i sprzęt chłodzący zmniejszają ładowność w porównaniu do zwykłych kontenerów) oraz wyższe koszty – zarówno zakupu, jak i frachtu (ze względu na zużycie energii). Konieczne jest też stałe zasilanie i monitoring, gdyż awaria agregatu może doprowadzić do zepsucia cennego ładunku. Mimo tych wyzwań kontenery chłodnicze stanowią podstawę światowej chłodniczej sieci dostaw, umożliwiając globalny handel produktami spożywczymi wymagającymi kontrolowanych warunków.
Kontenery z otwartym dachem (open top)
Kontener open top to kontener pozbawiony stałego dachu. Zamiast metalowego stropu posiada od góry otwór załadunkowy na pełną szerokość i długość, zabezpieczany plandeką (brezentową pokrywą) rozpinaną na stalowych belkach. Taki kontener umożliwia łatwy załadunek od góry za pomocą dźwigu – jest niezastąpiony, gdy przewozimy ładunki o ponadnormatywnej wysokości lub takie, których nie da się załadować przez standardowe drzwi. Przykłady to ciężkie maszyny przemysłowe, transformatory, elementy konstrukcji stalowych, a także ładunki sypkie ładowane luzem (np. złom, węgiel) wsypywany bezpośrednio z góry. Kontenery open top występują zazwyczaj w długościach 20′ i 40′, często także w wersji High Cube (podwyższonej), aby zmaksymalizować dostępną przestrzeń.
Zalety takiego kontenera to przede wszystkim uniwersalność w przewozie ładunków wysoko przekraczających standardowe wymiary. Zdemontowanie dachu (zwinięcie plandeki) pozwala załadować obiekt, który może nawet nieco wystawać ponad nominalną wysokość kontenera. Kontener nadal chroni boki ładunku i umożliwia piętrzenie w stosy na statku po założeniu pokrycia dachowego. Wady to nieco niższa sztywność konstrukcji (brak stałego dachu nieco osłabia bryłę) oraz większa ekspozycja ładunku na warunki atmosferyczne – plandeka chroni przed deszczem, ale nie zapewnia takiej izolacji termicznej i szczelności jak stalowy dach. Ponadto dostępność open topów jest mniejsza niż kontenerów zamkniętych, co może wpływać na wyższy koszt ich użycia.
Kontenery platformowe (flat rack)
Kontener platformowy typu flat rack to kontener pozbawiony dachu i ścian bocznych, posiadający jedynie podłogę oraz dwie ściany czołowe na krótszych bokach. Ściany te bywają składane lub demontowalne, co ułatwia załadunek z boku oraz pozwala na przewóz towarów szerszych niż standardowa szerokość kontenera. Flat racki produkowane są najczęściej w rozmiarach 20′ i 40′ z mocnej stali, aby wytrzymać bardzo duże obciążenia. Przeznaczone są do transportu ciężkich, ponadgabarytowych ładunków, takich jak pojazdy wojskowe, elementy infrastruktury (np. fragmenty mostów, turbiny), duże maszyny budowlane czy nawet sekcje prefabrykowanych budynków.
Zaletą kontenerów flat rack jest możliwość przewozu ładunków ponadgabarytowych o wymiarach lub masie przekraczających możliwości zwykłego kontenera. Brak ścian oznacza, że ładunek może wystawać na boki lub do góry, a solidna platforma zapewnia stabilne mocowanie ciężarów (na podłodze rozmieszczono uchwyty do pasów i łańcuchów). Dodatkowo kilka flat racków można zestawić obok siebie, tworząc większą platformę dla wyjątkowo szerokiego obiektu (choć taka operacja jest skomplikowana logistycznie). Wadą jest całkowity brak ochrony przed pogodą – ładunek na flat racku jest narażony na deszcz, wiatr i sól morską, dlatego często zabezpiecza się go dodatkowymi plandekami. Sam kontener tego typu jest też cięższy i mniej dostępny niż standardowy, co przekłada się na wyższe koszty frachtu. Mimo to, w przewozach niektórych towarów flat rack bywa jedyną opcją kontenerową pozwalającą uniknąć droższego transportu specjalistycznego (np. statkiem typu heavy-lift lub jako ładunek ponadgabarytowy na pokładzie).
Kontenery cysternowe (tank)
Kontener cysternowy (ang. ISO tank container) to specjalistyczny kontener przeznaczony do przewozu płynów i gazów luzem. Konstrukcyjnie składa się z cylindrycznego zbiornika wykonanego ze stali (często nierdzewnej) umieszczonego w ramach o standardowych wymiarach kontenera 20-stopowego. Taka intermodalna cysterna może przewozić zarówno produkty niebezpieczne (chemikalia, kwasy, paliwa) jak i spożywcze (np. oleje roślinne, soki, wino) czy inne ciecze przemysłowe. Pojemność typowego kontenera-cysterny to około 25 tysięcy litrów.
Zaletą tego rozwiązania jest bezpieczny i efektywny transport cieczy – w porównaniu z przewozem w setkach beczek, użycie jednej dużej cysterny ogranicza ryzyko wycieku i upraszcza załadunek oraz rozładunek (odbywa się on pompami przez zawory w kontenerze). Tank-kontener zachowuje standardowe wymiary, więc może być przeładowywany jak każdy inny, co umożliwia łatwe przenoszenie płynnych ładunków między statkiem, koleją a ciężarówką. Nowoczesne kontenery cysternowe wyposażone są w zawory bezpieczeństwa, często też w płaszcz izolacyjny; niektóre mają systemy podgrzewania (np. parowego lub elektrycznego), by utrzymać lepkość przewożonego produktu. Wadami są wyższe koszty zakupu i utrzymania (specjalistyczna konstrukcja musi spełniać rygorystyczne normy) oraz mniejsza uniwersalność – cysterna przewiezie tylko jeden rodzaj ładunku na raz, a przed zmianą produktu wymaga dokładnego czyszczenia i certyfikacji. Ponadto pusty kontener-cysterna to spory nieużyteczny ciężar, dlatego tak istotne jest planowanie rotacji, by jak najmniej przewozić je bez ładunku.
Kontenery wentylowane
Kontener wentylowany to odmiana kontenera ogólnego wyposażona w system wentylacji – pasywnej (otwory wentylacyjne) lub aktywnej (wentylatory). Zapewnia cyrkulację powietrza wewnątrz podczas transportu, co jest istotne dla ładunków wrażliwych na kondensację wilgoci i zaduch. Tego typu kontenery stosuje się przy towarach wymagających wymiany powietrza ze względu na ich charakter – np. ziarna kawy i kakao w workach, ryż, orzechy, nasiona. Wentylacja zapobiega gromadzeniu się pary wodnej wewnątrz skrzyni – nadmiar wilgoci wydostaje się na zewnątrz, a do środka napływa świeże powietrze, co chroni towar przed zawilgoceniem i pleśnią. Kontenery wentylowane zachowują pełną wytrzymałość konstrukcji i szczelność na opady – otwory są zaprojektowane tak, by deszcz nie dostawał się do środka.
Ograniczeniem użycia wentylowanych kontenerów jest to, że nie nadają się do ładunków wymagających całkowicie suchego środowiska (bo z definicji dopuszczają przepływ powietrza z zewnątrz) ani do utrzymywania precyzyjnej temperatury jak w chłodniach. Są też mniej dostępne niż standardowe dry vany, zatem ich rezerwacja musi być uwzględniona z wyprzedzeniem w planowaniu transportu.
Kontenery do ładunków sypkich (bulk)
Do przewozu suchych ładunków masowych, takich jak zboża, cukier, pasze czy granulaty przemysłowe, wykorzystuje się kontenery do ładunków sypkich (tzw. bulk containers). Z zewnątrz przypominają zwykły kontener 20′ lub 40′, ale mają specjalne elementy: na dachu znajdują się klapy lub włazy do nasypywania produktu, a w dolnej części – otwory lub zasuwy do grawitacyjnego wyładunku. Często stosuje się również dodatkowe wkłady – duże worki typu liner bag montowane wewnątrz kontenera, które tworzą szczelną wyściółkę dla sypkiego towaru. Taki worek upraszcza rozładunek (można go rozciąć lub zdemontować, wysypując zawartość) i chroni kontener przed zabrudzeniem.
Zaletą kontenerów bulk jest możliwość przewozu ładunków sypkich luzem bez potrzeby pakowania ich w mniejsze opakowania. Cała partia towaru może być przemieszczona w jednej jednostce, co eliminuje przeładunki pośrednie – np. z silosu w gospodarstwie zboże trafia bezpośrednio do kontenera, następnie jest przewiezione koleją lub statkiem i wyładowane u odbiorcy prosto do jego silosu. Standaryzacja kontenerowa zapewnia przy tym pełne korzyści intermodalności również dla towarów masowych. Wadą jest natomiast konieczność posiadania odpowiedniej infrastruktury do obsługi – do napełniania potrzebne są elewatory zbożowe lub taśmociągi, a do rozładunku urządzenia wspomagające grawitacyjne wysypanie (np. stelaże do przechyłu kontenera) bądź systemy ssące. Po przewozie jednego rodzaju ładunku sypkiego kontener trzeba też dokładnie oczyścić, chyba że użyto wyściółki jednorazowej. Kontenery do towarów masowych stanowią mniejszy odsetek floty, ale w logistyce np. sektora spożywczego czy chemicznego są bardzo istotne.
Kontenery półwysokościowe (half-height)
Kontenery półwysokościowe mają około połowy standardowej wysokości (ok. 1,3 m zamiast 2,6 m), przy zachowaniu pełnej długości i szerokości kontenera ISO. Wyglądają jak „przycięte” kontenery – niższe skrzynie, często otwarte od góry lub ze zdejmowanym dachem. Powstały z myślą o transporcie bardzo ciężkich ładunków, którym niepotrzebna jest pełna wysokość. Typowe zastosowania to przemysł wydobywczy i budownictwo: przewóz urobku kopalnianego, rudy, węgla, kamieni, gruzu, metali w sztabach itp. – czyli materiałów o dużej masie przy stosunkowo małej objętości. Kontener półwysokościowy dzięki zredukowanej kubaturze można bezpiecznie wypełnić niezwykle ciężkim materiałem nie przekraczając dopuszczalnej masy całkowitej. Załadunek i rozładunek takiego kontenera bywa łatwiejszy – ze względu na niższe burty można używać koparek i ładowarek czołowych, a niższy środek ciężkości poprawia stabilność przy podnoszeniu.
Zaletą half-heightów jest dostosowanie do specyfiki ładunków o ekstremalnej gęstości. Są bardziej poręczne w manipulacji takim towarem niż standardowe kontenery (niższy środek ciężkości, możliwość ustawienia dwóch półwysokościowych jeden na drugim w miejscu jednego standardowego). Wadą jest z kolei bardzo ograniczona uniwersalność – niski kontener nie sprawdzi się przy większości typowych ładunków drobnicowych, ponieważ przestrzeń byłaby niewykorzystana. Kontenery półwysokościowe to rozwiązanie czysto specjalistyczne, spotykane głównie w rejonach, gdzie dominuje transport surowców o dużej gęstości (np. w kopalniach Australii czy Afryki Południowej).
Trendy i innowacje 2024-2025 w logistyce kontenerowej
Ostatnie lata przynoszą w branży kontenerowej dynamiczne zmiany, napędzane rozwojem technologii oraz dążeniem do większej efektywności i zrównoważenia. Poniżej omówiono najważniejsze trendy i innowacje, które kształtują logistykę kontenerową w latach 2024–2025.
Cyfryzacja i inteligentne kontenery
Branża przewozów kontenerowych przechodzi przyspieszoną cyfryzację procesów. Przewoźnicy i spedytorzy wdrażają elektroniczne systemy dokumentacji – przykładem jest rosnąca akceptacja elektronicznych konosamentów (eBL, electronic Bill of Lading), które zastępują tradycyjne papierowe dokumenty przewozowe. Według danych z 2024 roku udział e-dokumentów systematycznie rośnie, upraszczając formalności oraz skracając czas odpraw. Równolegle standardem stają się inteligentne kontenery wyposażone w urządzenia IoT (Internet of Things). Specjalne czujniki montowane na kontenerach monitorują w czasie rzeczywistym takie parametry jak lokalizacja GPS, temperatura wewnątrz, wilgotność, wstrząsy czy nawet to, czy drzwi zostały otwarte. Dane z sensorów są przesyłane za pośrednictwem sieci satelitarnej lub komórkowej do platform cyfrowych. Dzięki temu właściciel ładunku może na bieżąco śledzić warunki przewozu – istotne np. dla kontenerów chłodniczych (kontrola temperatury) czy kontenerów z towarem wrażliwym na wstrząsy. Inteligentne systemy pozwalają także szybciej reagować na nieprzewidziane zdarzenia – alarm przy otwarciu drzwi może wskazywać próbę kradzieży, a wzrost temperatury w chłodni awarię agregatu, co umożliwia podjęcie działań zapobiegających stratom. Organizacje branżowe, takie jak Digital Container Shipping Association (DCSA), opracowują wspólne standardy dla rozwiązań cyfrowych, aby różne systemy były ze sobą kompatybilne. Cyfryzacja obejmuje również optymalizację operacji portowych – wdraża się platformy do automatycznego zarządzania ruchem kontenerów na terminalach oraz wykorzystuje big data i algorytmy AI do planowania tras statków i połączeń intermodalnych w sposób minimalizujący puste przebiegi. Ogólnie, w latach 2024–2025 automatyzacja informacyjna staje się filarem nowoczesnej spedycji kontenerowej, zwiększając przejrzystość łańcucha dostaw i obniżając koszty administracyjne.
Ekologiczne rozwiązania i zrównoważony rozwój
W odpowiedzi na wyzwania klimatyczne sektor transportu kontenerowego inwestuje w zrównoważony rozwój i redukcję emisji. Jednym z trendów są tzw. zielone korytarze żeglugowe – inicjatywy, w których całe połączenia morskie obsługiwane są statkami zasilanymi paliwami alternatywnymi o niskiej emisji CO₂. Przykładowo, pod koniec 2024 roku na Morzu Bałtyckim uruchomiono pilotażowy korytarz, gdzie statki kontenerowe wykorzystują biopaliwa (m.in. biogaz i HVO – uwodorniony olej roślinny), co pozwala zredukować emisje aż o 90% względem tradycyjnego paliwa. Równocześnie armatorzy modernizują floty – pojawiają się pierwsze kontenerowce napędzane skroplonym gazem ziemnym (LNG), metanolem, a nawet z eksperymentalnym napędem żaglowym (żagle rotorowe, latawce) wspomagającym napęd w celu oszczędzania paliwa. Porty również wdrażają ekologiczne praktyki: stosują zieloną energię do zasilania terminali, testują elektryczne ciągniki oraz dźwigi, a także oferują statkom możliwość podłączenia do prądu z lądu (cold ironing), by mogły wyłączać własne generatory podczas postoju. Kolejnym aspektem jest zarządzanie kontenerami w sposób przyjazny środowisku – coraz większy nacisk kładzie się na optymalizację rotacji kontenerów, aby unikać pustych przebiegów (dzięki lepszemu dopasowaniu eksportu do importu oraz rozwojowi giełd kontenerowych, na których przewoźnicy współdzielą nadwyżki kontenerów). Nie bez znaczenia są też innowacje materiałowe: prowadzi się prace nad bardziej trwałymi, a jednocześnie lżejszymi kontenerami (np. ze stali o wyższej wytrzymałości lub z kompozytów), co pozwoli zmniejszyć masę przewożoną „na pusto” i tym samym zużycie paliwa. W latach 2024–2025 kwestie ekologiczne przestają być tylko wizerunkowe – regulacje IMO (Międzynarodowej Organizacji Morskiej) dotyczące redukcji emisji zmuszają armatorów do konkretnych działań, a klienci coraz częściej oczekują „zielonych” rozwiązań logistycznych. Kontener staje się więc elementem szerszego ekosystemu, który ma być jak najbardziej neutralny klimatycznie.
Nowe konstrukcje i usprawnienia kontenerów
Innowacje dotyczą nie tylko procesów, ale i samych kontenerów jako fizycznych obiektów. Jednym z ciekawych rozwiązań ostatnich lat są składane kontenery. Klasyczny pusty kontener zajmuje tyle samo miejsca co pełny, co rodzi problemy przy ich magazynowaniu i powrotach „na pusto”. Rozwiązaniem są kontenery modułowe, które można złożyć (zredukować ich objętość) gdy są puste. Na rynku pojawiły się już prototypy i pierwsze serie takich jednostek – np. kontener „4FOLD”, który składa się do 1/4 swojej wysokości. Oznacza to, że cztery złożone kontenery można zstackować w przestrzeni jednego standardowego, co oszczędza miejsce na statkach i placach oraz obniża koszty relokacji pustych opakowań. Mimo dodatkowych mechanizmów kontenery składane są projektowane tak, by ich rozkładanie i składanie było szybkie i niewymagające specjalistycznego sprzętu. Inną innowacją konstrukcyjną są ulepszenia kontenerów chłodniczych – nowe agregaty chłodnicze zużywają mniej energii i wykorzystują czynniki chłodnicze o niższym potencjale cieplarnianym (co redukuje wpływ na klimat). Pojawiają się również kontenery z wbudowanymi systemami kontroli atmosfery (CA, Controlled Atmosphere), które oprócz temperatury regulują skład gazowy we wnętrzu (obniżenie tlenu, podwyższenie CO₂) w celu spowolnienia procesów dojrzewania owoców podczas transportu. Materiały wykorzystywane do budowy kontenerów też są doskonalone – np. stosuje się podłogi z tworzyw sztucznych lub kompozytów zamiast tradycyjnych drewnianych (są trwalsze i nie wymagają chemicznej impregnacji przeciw szkodnikom). Nawet tak prozaiczne elementy jak zamki kontenerowe są usprawniane – coraz częściej montuje się inteligentne zamknięcia z możliwością zdalnego sprawdzenia, czy kontener jest zamknięty i nienaruszony. Wszystkie te zmiany mają na celu uczynić kontener bardziej funkcjonalnym, bezpieczniejszym i tańszym w użytkowaniu.
Automatyzacja portów i rozwój infrastruktury
Wraz ze wzrostem skali transportu kontenerowego (największe kontenerowce przewożą już ponad 24 tysiące TEU jednorazowo) konieczne stało się dostosowanie infrastruktury oraz zwiększenie automatyzacji. Nowoczesne terminale kontenerowe wprowadzają coraz więcej autonomicznych urządzeń – automatyczne suwnice placowe i stackery same układają kontenery w blokach składowych według zoptymalizowanych algorytmów, z minimalną ingerencją człowieka. Ciągniki terminalowe przewożące kontenery między placem a nabrzeżem coraz częściej są elektryczne i sterowane komputerowo niczym roboty. Te zautomatyzowane terminale zwiększają przepustowość portów i skracają czas postoju statków. Równocześnie trwa rozbudowa infrastruktury portowej – wiele portów pogłębia kanały i baseny, wzmacnia nabrzeża oraz inwestuje w większe suwnice nabrzeżowe, by móc obsługiwać mega-kontenerowce najnowszej generacji. Przykładowo, porty w Europie i Azji rywalizują o miano najbardziej wydajnych hubów: port w Rotterdamie czy Singapurze wdrażają systemy predykcyjne do zarządzania ruchem statków, tak aby zawinięcia przebiegały sprawnie nawet przy bardzo dużym natężeniu. Na kolejowym i drogowym odcinku łańcucha dostaw również następują zmiany – powstają dedykowane suche porty i terminale intermodalne bliżej centrów logistycznych w głębi lądu, gdzie kontenery mogą być przekazywane między pociągiem a ciężarówką, odciążając same porty morskie. W planach wielu krajów (np. w ramach inicjatywy Nowego Jedwabnego Szlaku) jest budowa kolejnych centrów przeładunkowych oraz inteligentnych systemów zarządzania, co ma zapewnić płynność obsługi rosnącej liczby kontenerów w obiegu. W perspektywie 2025 roku priorytetem staje się więc infrastruktura pozwalająca sprostać rosnącej skali wymiany towarowej – zarówno w aspekcie fizycznym (większe statki i porty), jak i cyfrowym (integracja systemów wszystkich ogniw transportu).